Granule Coating System
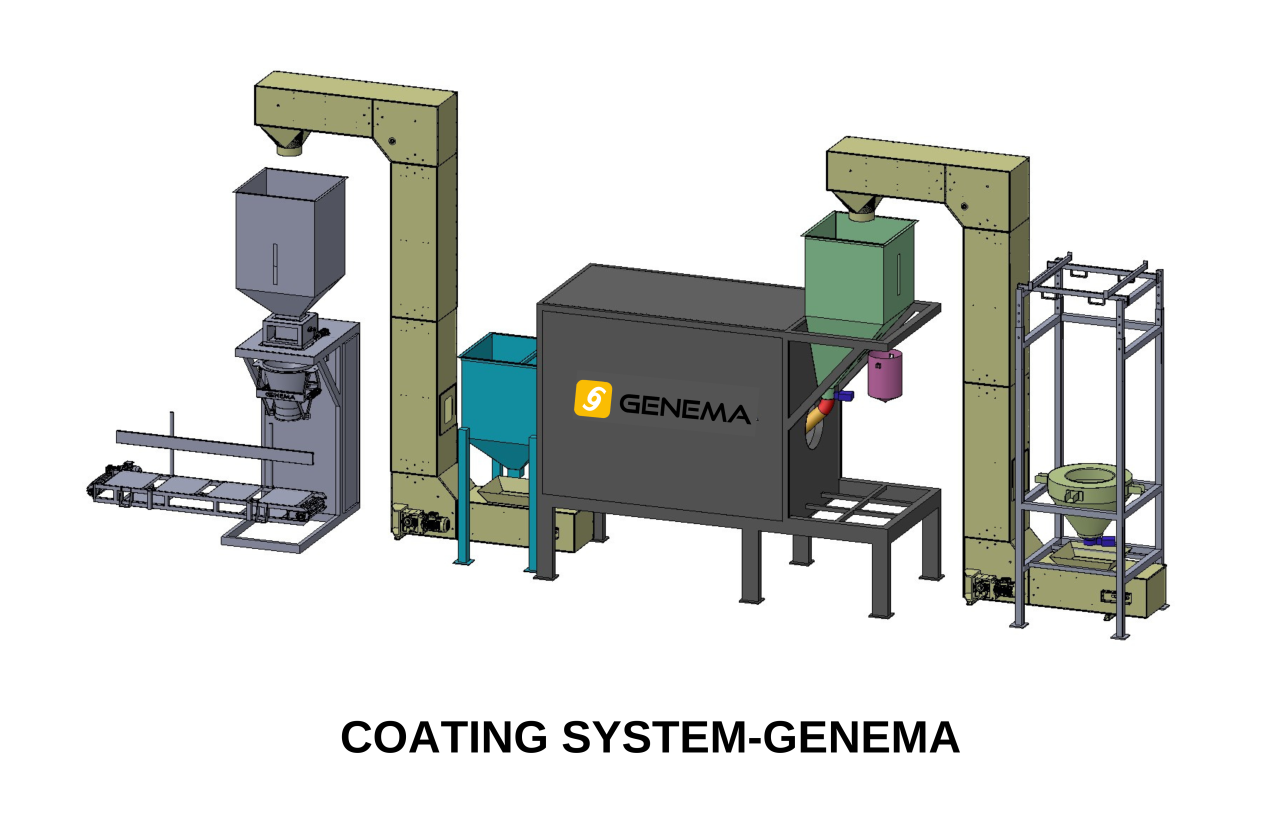
The granule coating process is essential for many industries. In the pharmaceutical industry, for example, it is very important to control the amount of release. Or, as in the case of granular fertilizer coating and seed coating, this process can be used to increase the product’s duration of action in the soil. Besides all these, it can be preferred in the food industry to increase the attractiveness of the product. Therefore, it has many different uses. The important thing is to install the most efficient system considering the place and conditions of use.
Fertilizer Granule Coating
For the fertilizer industry, granular coating is of particular importance. Because the intensive use of chemical fertilizers in the world, especially in the last 30-40 years, has led to increased soil salinity and loss of organic and biological substances. For this reason, no matter how much chemical fertilizer is used, it is difficult to keep the fertilizer in the soil. For example, nitrogen fertilizers disappear very quickly in the form of nitrate. One of the best strategies to avoid this is to coat conventional fertilizers with a new generation of release-retarding biomaterials. In this way, slow-release and controlled-release fertilizers can be produced. Also, not only chemical fertilizers such as Urea and DAP need to be coated. Organic fertilizer granules/micro-granules or organomineral granules can be similarly coated to improve their properties.
Coating Materials for Fertilizer Industry
Fertilizer coatings are used to enhance nutrient release, improve handling, and reduce environmental losses. There are many different types and structures of coating materials. For example, polymeric coating materials used for slow and controlled release are PLA, PHA and PU etc. If desired, these can also be classified as biodegradable and non-biodegradable. In addition to polymeric coatings, elemental coatings such as sulfide coatings are sometimes applied in industry. New formulations can also be developed for coatings. For example, paraffin wax can play an anti-caking role and kaolin can be used as a moisture absorbent. In short, new solutions can be produced according to need.
Seed Coating
The main benefits of seed coating have increased the frequency of its application in recent years. Here are some reasons:
- Coated seed has good flow. So it is suitable for mechanical sowing
- This type of seed provides better moisture retention
- Seed coating material protects the seed against environmental stress factors
- Coating process improves germination and seedling formation
Materials for Seed Coating
Seed coating materials vary depending. For example, talc and Bentonite can be preferred as fillers. In addition, NPK or micronutrients create a nutrient-rich environment. For many cases, colorants such as iron oxide are added to give the product character. Briefly, there are many possibilities.
Coating System Components
A typical granular coating system consists of the following components:
- Big-bag discharge unit: Automatically feeds granular raw materials into the system.
- Material dosing system: Feeds the coating material into the system as desired.
- Coating machine: Realizes a homogeneous and efficient coating process.
- Elevators: Transports materials between components.
- Packaging system: Packs coated granules.
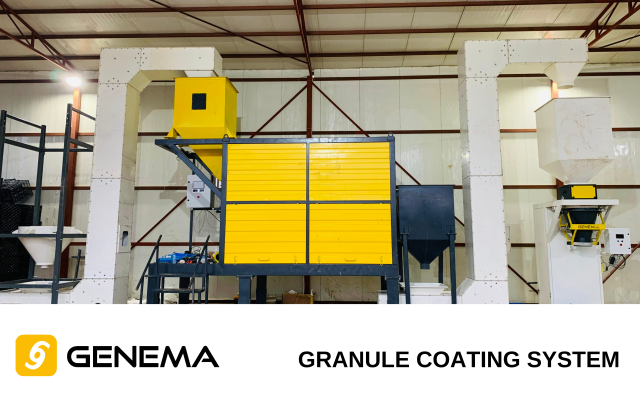